ANALYSE DER
GESAMTBETRIEBSKOSTEN (TCO)
Gemäß fünf Lean-Prinzipien
Wertstrom kartieren: Verfolgen Sie die Schritte und Aktivitäten, die erforderlich sind, um ein Produkt an den Punkt zu bringen, an dem es benötigt wird.
Wert bestimmen: Bestimmen Sie, welche Aktivitäten Wert für Ihre Kunden bringen und welche nicht (Wertschöpfung vs. nicht wertschöpfend oder NVA). Unser Schwerpunkt: Finden Sie Lösungen, die NVA-Berührungen eliminieren oder reduzieren.
Flow schaffen: Nachdem die NVAs eliminiert wurden, lassen Sie die wertschöpfenden Schritte nahtlos zusammenfließen, mit minimalem Reiseaufwand oder Unterbrechungen. Der vom Lieferanten verwaltete Nachschub am Einsatzort ist hier ein Schlüsselkonzept.
Pull statt Push: Implementieren Sie Systeme, um Inventar nur bei Bedarf einzuholen (z. B. Supermärkte und Kanban, einschließlich elektronischer Signaleinrichtungen).
Nach Perfektion streben – 6S: Mit dem 6S-Konzept Produktivität fördern durch Sortieren, Systematisieren, Reinigen, Standardisieren, Erhalten und Sicherheit.“
Als Teil unserer Analyse der Gesamtbetriebskosten (TCO) nutzen wir eine Lean-Strategie, die als DMAIC bekannt ist, um einen Flow zu schaffen, Abfall zu beseitigen und Effizienz in der Lieferkette zu fördern.
Im Rahmen dieses Prozesses arbeitet unser Lean-Solutions-Team mit den wichtigsten Mitarbeitenden in Ihrem Unternehmen zusammen (Werksleiter, Wareneingangsmitarbeiter, Inspektoren, Einkäufer usw.), um den Produktfluss in Ihrem System zu erfassen, Verschwendungsbereiche zu ermitteln und Ideen zur Kostensenkung innerhalb Ihrer Lieferkette vorzuschlagen.
- Schritt 1 -
DEFINITION
Ziele und Herausforderungen erörtern
Historische Daten sammeln
Einen vollständigen Produktpfad abbilden
- Schritt 2 -
MESSUNG
Eine Basis-Gesamtkostenberechnung erstellen
Basislinie grafisch darstellen, um zukünftige Verbesserungen zu messen
- Schritt 3 -
ANALYSE
Schritte ohne Wertzuwachs ermitteln
Abfallquellen identifizieren
Zusammenfassung eines zukünftigen Zustands erstellen
- Schritt 4 -
VERBESSERUNG
Ergebnisse des Ist-Zustandes präsentieren
Prozessoptimierungen empfehlen und umsetzen
- Schritt 5 -
KONTROLLE
Vierteljährliche Revisionstreffen
Kosteneinsparungen und künftige Einsparmöglichkeiten präsentieren
VERSCHWENDUNG BESEITIGEN UND
DIE EFFIZIENZ DER LIEFERKETTE STEIGERN
Ergebnisse stehen im Mittelpunkt
Fahren Sie mit der Maus über die Boxen, um mehr zu erfahren

Gesamtbetriebskosten
Ein 360-Grad-Ansatz zur Kostensenkung durch Lieferantenkonsolidierung, Verbrauchskontrolle, SKU-Rationalisierung, Produktsubstitution und Reduzierung von Lagerbeständen, Arbeitsaufwand, Frachten und Bestellungen.
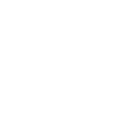
Produktivität
Einsatz von Strategien wie Just-in-Time-Inventar, vom Lieferanten verwaltetes Inventar (VMI), Lieferung an den Einsatzort, Teile-Kitting und Automatisierung der Materialausgabe (z. B. Automaten oder automatisierte Behälter), um das Personal auf wertschöpfende Tätigkeiten zu konzentrieren.
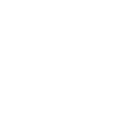
Bestand
Einführung von Systemen zur effizienten Reduzierung von verfügbarem Lagerbestand bei gleichzeitiger Identifizierung und Beseitigung veralteter/überflüssiger Ressourcen. Zu den Optionen gehört ein Vor-Ort-Modell, bei dem das Inventar und das Fachpersonal von Fastenal zur Verfügung gestellt werden, um den Lageraufwand zu bewältigen.
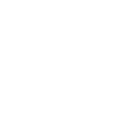
Sichtbarkeit
Nutzen Sie die Vor-Ort-Lösungen von Fastenal, um aussagekräftige Berichte zu erstellen, die auf Ihre Geschäftsziele abgestimmt sind. Nutzen Sie das FAST 360°-Berichtsdashboard, um Einkaufs-/Nutzungstrends zu analysieren und Ihr Fastenal-verwaltetes Inventar vor Ort (Produkte, Standorte und Mengen) zu visualisieren.

Vom Konzept zur kontinuierlichen Verbesserung
Wir beginnen mit einer Standortanalyse (TCO-Analyse) und arbeiten mit den Akteuren der Lieferkette zusammen, um Ihren Betrieb zu verstehen, Verschwendungsquellen zu identifizieren und eine Lösung zu entwickeln, mit der Sie Ihren zukünftigen Wunschzustand erreichen können. Nach der anfänglichen Beratung und der Entwicklung der Lösung implementieren unsere Fachleute das Programm vor Ort und führen regelmäßige Audits durch, um eine kontinuierliche Verbesserung zu gewährleisten.
Wir konzentrieren uns auf die acht wichtigsten Verschwendungsarten
Mit dem DMAIC-Prozess lassen sich acht Verschwendungsquellen identifizieren, die Ihre Produktivität beeinträchtigen können.
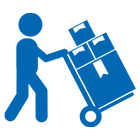
Transport
Zu viele Produktbewegungen innerhalb des Standorts
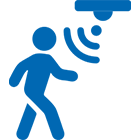
Bewegung
Unnötige Personalbewegungen im Zusammenhang mit Inventar
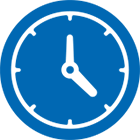
Warten
Ausfallzeiten wegen fehlendem Zugang zu benötigten Teilen oder Werkzeugen
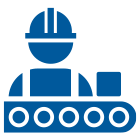
Überproduktion
Lieferung über Bedarf
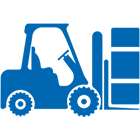
Bestand
Überschüssige, veraltete oder unnötige Teile in der Lieferkette

Zusätzliche Bearbeitung
Schritte, die bei der Ausführung einer Funktion anfallen und nicht zur Wertschöpfung beitragen
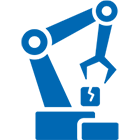
Mängel
Produkt entspricht nicht den Anforderungen
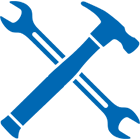
Ungenutzte Arbeitskräfte
Verschwendung von Zeit und Talent für nicht wertschöpfende Tätigkeiten