TOTAL COST OF OWNERSHIP
(TCO) ANALYSIS
Guided by Five Lean Principles
Map the Value Stream: Trace the steps and activities required to bring a product to the point where it’s needed.
Determine Value: Identify which activities bring value to your customers and which do not (value-add vs. non-value-add, or NVA). Our focus: Find solutions that eliminate or reduce NVA touches.
Create Flow: After eliminating NVAs, make the value-added steps flow together seamlessly, with minimal travel or stoppages. Vendor-managed point-of-use supply is a key concept here.
Push for ‘Pull’: Implement systems to pull inventory into use only as needed (e.g. supermarkets and Kanban, including electronic signaling devices).
Pursue Perfection – 6S: Promote productivity vis Sort, Set in Order, Shine, Standardize, Sustain and Safety.
As part of our Total Cost of Ownership (TCO) Analysis, we utilize a Lean strategy known as DMAIC to create flow, eliminate waste and drive supply chain efficiencies.
As part of the process, our Lean Solutions team will work with key personnel in your organization (the plant manager, receiving personnel, inspectors, buyers, et al.) to map how product flows through your system, identify areas of waste, and propose ideas to drive down costs within your supply chain.
- Step 1 -
DEFINE
Discuss objectives and challenges
Collect historical data
Map a complete path of product
- Step 2 -
MEASURE
Create a baseline total cost
Graph baseline to measure future improvements
- Step 3 -
ANALYSE
Determine which current steps are non-value-added
Identify sources of waste
Create a future state summary
- Step 4 -
IMPROVE
Present current state findings
Recommend & implement process improvements
- Step 5 -
CONTROL
Quarterly review meetings
Present cost savings & future savings opportunities
ELIMINATING WASTE AND DRIVING
SUPPLY CHAIN EFFICENCY
Focusing on Results
Roll over each box to learn more

Total Cost of Ownership
Taking a 360-degree approach to reduce expenditures through vendor consolidation, consumption controls, SKU rationalization, product substitutions, and reductions in inventory, labor, freight, and purchase orders.
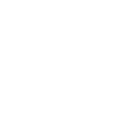
Productivity
Using strategies like just-in-time inventory, vendor-managed inventory (VMI), point-of-use delivery, parts kitting, and supply automation (e.g., vending or automated bins) to keep employees focused on value-adding activities.
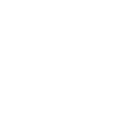
Inventory
Implementing systems to confidently reduce on-hand inventory while identifying and drawing down obsolete/redundant assets. Options include an onsite model, providing Fastenal-owned inventory and dedicated experts to shoulder inventory burdens.
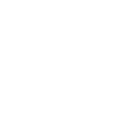
Visibility
Leveraging Fastenal’s point-of-use solutions to provide relevant reporting aligned with your business goals. Utilize the FAST 360° reporting dashboard to analyze purchasing/usage trends and visualize your Fastenal-managed inventory on hand (products, locations, and amounts).

From Concept to Continuous Improvement
We begin with a site assessment (TCO Analysis) and collaborate with supply chain stakeholders to understand your operation, identify sources of waste, and craft a solution to achieve your desired future state. Along with providing initial consultation and solution design, our experts will physically implement the program and periodically audit the site to drive continuous improvement.
Targeting Eight Central Wastes
The DMAIC process brings visibility to eight sources of waste that could be hindering your productivity.
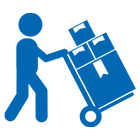
Transportation
Excessive product movement throughout a facility
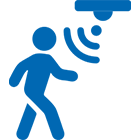
Motion
Non-essential employee movement related to inventory
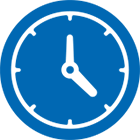
Waiting
Downtime caused by a lack of access to needed parts or tools
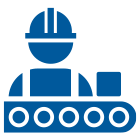
Overproduction
Supplying more than demand
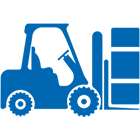
Inventory
Surplus, obsolete or unnecessary parts in the supply chain

Extra Processing
Non-value-added steps to complete a function
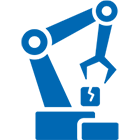
Defects
Product that doesn’t meet requirements
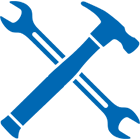
Non-Utilized Labor
Time and talent spent on non-value-added activities