ANALYSE DU COÛT TOTAL DE POSSESSION
(TCO)
Guidée par cinq principes Lean
Cartographie de la chaîne de valeur ajoutée : déterminez les étapes et les activités nécessaires pour amener un produit au point d’utilisation.
Détermination de la valeur : identifiez les activités qui apportent de la valeur à vos clients et celles qui n’en apportent pas (valeur ajoutée par rapport à non-valeur ajoutée, ou NVA). Notre priorité : trouver des solutions qui éliminent ou réduisent la NVA.
Création d’un flux : après avoir éliminé les NVA, faites en sorte que les étapes à valeur ajoutée s’enchaînent de manière fluide, avec un minimum de déplacements ou d’arrêts. L’approvisionnement au point d’utilisation géré par le fournisseur joue ici un rôle essentiel.
Remplacement du système Push par un système Pull : Mettez en place des systèmes permettant d’utiliser les stocks uniquement en cas de besoin (ex. : kanban et supermarché, y compris des dispositifs de signalisation électronique).
Visez la perfection – ORDRES : gagnez en productivité en respectant les principes suivants : ordonner, ranger, dépoussiérer, rendre évident, être rigoureux, sécuriser.
Dans le cadre de notre analyse du coût total de possession (direct/indirect) (TCO), nous utilisons une stratégie Lean connue sous le nom de DMAIC pour créer une dynamique, éliminer les gaspillages et optimiser la chaîne d’approvisionnement.
Tout au long de ce processus, notre équipe Lean Solutions collaborera avec le personnel clé de votre organisation (directeur d’usine, personnel de réception, inspecteurs, acheteurs, etc.) pour cartographier le cheminement des produits dans votre système, identifier les sources de gaspillage et proposer des idées pour réduire les coûts au sein de votre chaîne d’approvisionnement.
- Étape 1 -
DÉFINITION
Discuter des objectifs et des défis
Collecter des données historiques
Tracer un parcours complet du produit
- Étape 2 -
MESURE
Créer un coût total de référence
Graphique de référence pour mesurer les améliorations futures
- Étape 3 -
ANALYSE
Déterminer les étapes actuelles qui n'apportent pas de valeur ajoutée
Identifier les sources de gaspillage
Créer un résumé de l'état futur
- Étape 4 -
AMÉLIORATION
Présenter les résultats de l'état actuel
Recommander et mettre en œuvre des améliorations de processus
- Étape 5 -
CONTRÔLE
Réunions d'évaluation trimestrielles
Réductions de coûts actuelles et possibilités d'économies futures
ÉLIMINATION DES GASPILLAGES ET PILOTAGE
DE L’EFFICACITÉ DE LA CHAÎNE D’APPROVISIONNEMENT
Focalisation sur les résultats
Passez la souris sur chaque case pour en savoir plus

Coût total de possession
Adopter une approche à 360 degrés pour réduire les dépenses en agissant sur les leviers suivants : consolidation des fournisseurs, contrôle de la consommation, rationalisation des UGS, substitution des produits et réduction des stocks, de la main-d’œuvre, du fret et des commandes d’achat.
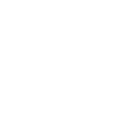
Productivité
Le recours aux stratégies telles que la gestion des stocks juste à temps (JIT), la gestion des stocks par le fournisseur (VMI), la livraison au point d’utilisation, le kitting des pièces détachées et l’automatisation de l’approvisionnement (par exemple à l’aide de distributeurs automatiques ou de bacs automatisés) permet de maintenir l’attention des employés sur les activités à valeur ajoutée.
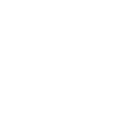
Stock
Mettre en œuvre des systèmes permettant de réduire en toute confiance les stocks disponibles tout en identifiant et en réduisant les actifs obsolètes/redondants. Les options incluent un modèle sur site, en fournissant des stocks appartenant à Fastenal et des experts dédiés pour prendre en charge les tâches fastidieuses liées à la gestion des stocks.
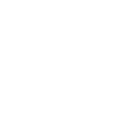
Visibilité
Exploiter les solutions Fastenal au point d’utilisation pour fournir un reporting pertinent aligné sur vos objectifs métier. Utilisez le tableau de bord de reporting FAST 360° pour analyser les tendances d’achat/d’utilisation et visualiser vos stocks gérés par Fastenal (produits, emplacements et quantités).

Du concept à l'amélioration continue
Nous commençons par une évaluation du site (analyse du coût total de possession) et collaborons avec les acteurs de la chaîne d’approvisionnement pour comprendre votre fonctionnement, identifier les sources de gaspillage et élaborer une solution qui vous permettra d’atteindre l’état futur souhaité. En plus de la consultation initiale et de la conception de la solution, nos experts mettront physiquement en œuvre le programme et procéderont périodiquement à des audits du site visant à assurer une amélioration continue.
Cibler huit sources principales de gaspillage
Le processus DMAIC permet de mettre en évidence huit sources de gaspillage susceptibles d’entraver votre productivité.
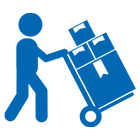
Transport
Mouvements excessifs de produits dans une installation
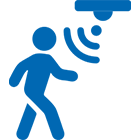
Déplacement
Mouvements de personnel non essentiels liés aux stocks
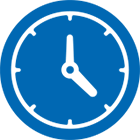
Temps d'attente
Temps d’arrêt causé par le manque d’accès aux pièces ou aux outils nécessaires
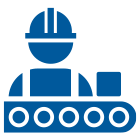
Surproduction
Fournir plus que la demande
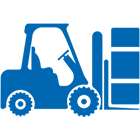
Stock
Pièces excédentaires, obsolètes ou inutiles dans la chaîne d’approvisionnement

Traitement supplémentaire
Étapes à non-valeur ajoutée pour compléter une fonction
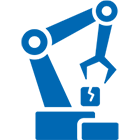
Défauts
Produit ne répondant pas aux exigences
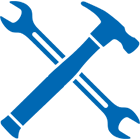
Main-d'œuvre non utilisée
Temps et talents consacrés à des activités à non-valeur ajoutée